Z nutnosti ochránit své zaměstnance, kteří pracují na dodávkách pro extrémně náročné zákazníky z leteckého průmyslu, před koronavirem, udělali slibně se rozvíjející branži. Když zjistili, že je nedostatek ochranných pomůcek, začali na jaře pracovat na projektu vlastní ochranné masky. Od prvních prototypů na nich bylo uděláno více než 100 modifikací a do vývoje investovali přes 100 milionů korun. Nedostatek filtrů je donutil vyrábět si vlastní. Každý z nich je testován, jestli splňuje normy převyšující standard FFP 3. Zachytí 99,995 % virů a bakterií. Jejich výrobky nyní chrání lékařský personál, hasiče, policisty či příslušníky Vězeňské služby ČR.
Vidina přerušení práce jeho firmy z důvodu nákazy koronavirem byla na jaře pro ředitele Workpress Aviation (WPA) Jiřího Heckela natolik nepřípustná, že když zjistil, že respirátory není možné nikde na světě koupit, rozhodl se se svým týmem nějaké navrhnout a vyrobit.
„Spočítali jsme si, že abychom ochránili naše zaměstnance respirátory FFP 3, vyšlo by to asi na 4 miliony měsíčně, jsou totiž jednorázové a máme okolo 300 zaměstnanců. Navíc pak byl zákaz jejich prodeje mimo zdravotnictví. Chtěli jsme něco trvalejšího s vysokou účinností. Byli jsme si samozřejmě vědomi toho, že po takovém výrobku bude poptávka i z řad zdravotníků a všech, kdo pracují v terénu,“ říká Heckel. „Když se podívám zpětně, tak současné masky jsou s porovnáním s prvními prototypy úplně jinde. I teď nejsem stoprocentně spokojený, i když je to nesmírný posun kupředu a na naše masky slyšíme jen positivní ohlasy. Už se to téměř blíží k tomu, s čím budu spokojený, proto dále pokračujeme ve vývoji a vylepšování masek,“ říká Heckel s tím, že je perfekcionista, takže je mu máloco dobré.
Kromě ochrany zdraví jejich zaměstnanců a zachování kontinuity výroby, chtěl Heckel se svým týmem také pomoc zdravotníkům a dalším lidem, kteří s pandemií bojují v první linii. „Od začátku spolupracujeme s Fakultní nemocnicí Plzeň. Připomínky jejich lékařů jsou k nezaplacení, protože dokážou říct, co je špatně, či co je dobré, ale chtělo by to jen trochu upravit. Naši polomasku testovalo několik desítek zaměstnanců nemocnice a nikdo z nich se nenakazil. Poté si objednali 500 kusů a posléze dalších 1.600. Chtějí ochránit všechny zaměstnance. Stejné výsledky vidíme u našich zaměstnanců. V druhé vlně naši zaměstnanci nosili již naše masky, ale kvůli náladě ve společnosti jsme nošení masek nenařizovali. Zaměstnanci tak nosili i respirátory KN95, nebo roušky. Řada z nich pak onemocněla. Následně jsme nařídili nošení našich masek, které zaměstnanci dostali a od té doby nemáme nikoho nakaženého,“ odhaluje praktické výsledky Jiří Heckel.
Mohlo by vás zajímat
Flexibilita výroby se ukázala hlavní výhodou
Hlavní výhodou při vývoji nového produktu se ukázala pružnost výroby WPA. Na té si firma zakládá od samého začátku. „Naší specializací je výroba dílů pro letecký průmysl. Od začátku jsme neodmítali žádné zakázky. Naše interní pravidlo bylo nikdy zákazníkovi neříct ne a vyjít mu maximálně vstříc. Postupem času jsme dokupovali stroje potřebné pro výrobu a pak jsme se rozhodli, že chceme mít vše pod jednou střechou. Budovu, kde máme kanceláře i hlavní výrobu dílů pro letecký průmysl, máme asi pět let,“ říká Heckel v zasedací místnosti, odkud je vidět do výrobní haly.
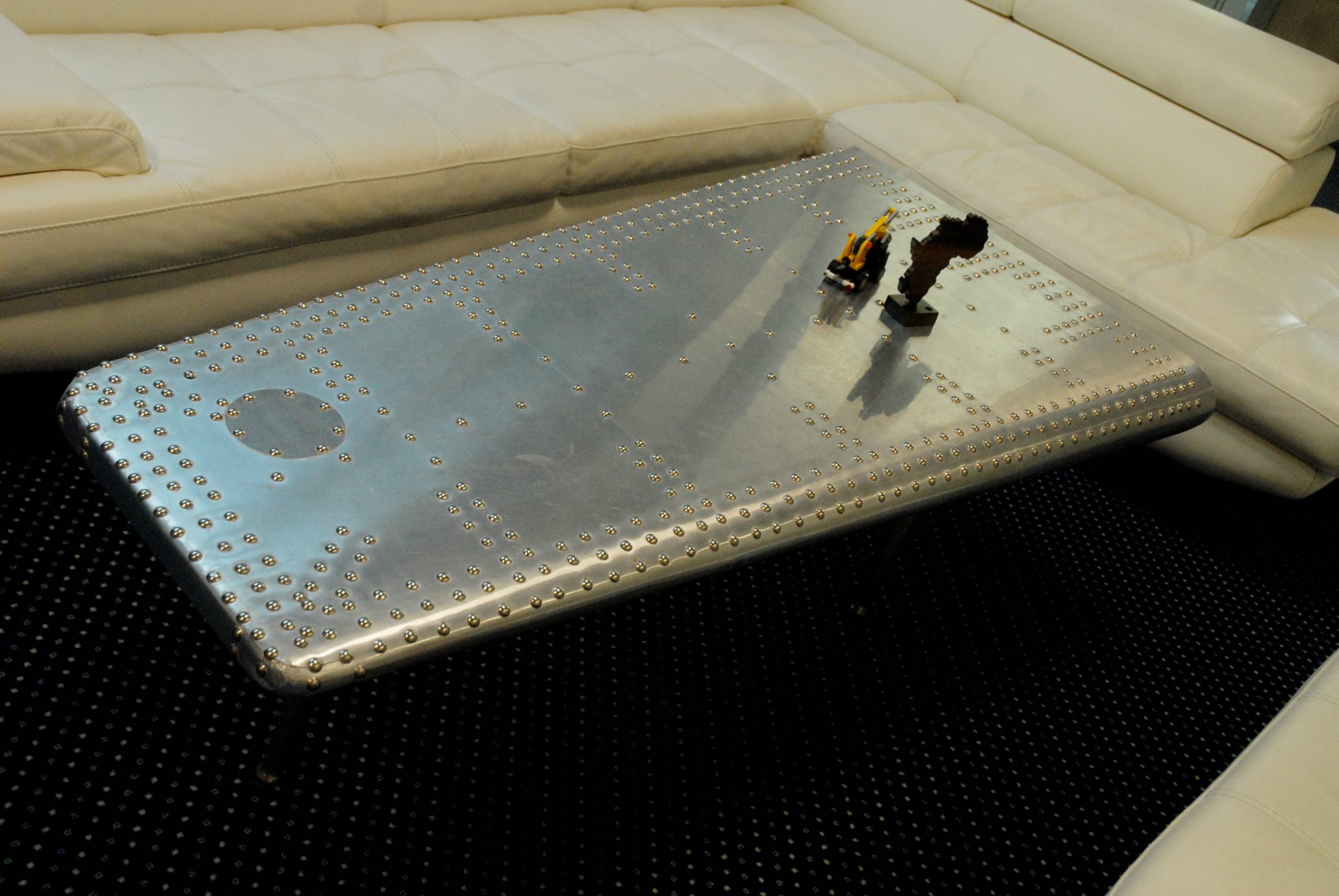
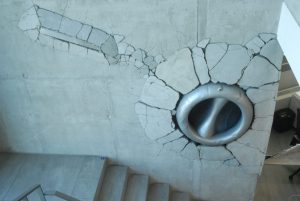
Pokud by návštěvník pochyboval, čím se firma zabývá, napoví mu hned vedle recepce čumák letadla „zabořený“ do betonové stěny. Evokuje letadlo „zapíchnuté“ zvenku do kancelářské budovy. Pozornému návštěvníkovi neunikne ani „vyboulenina“ v místě křídla aeroplánu. Působí to tak trochu jako ironie osudu. Jeden ze zakladatelů firmy před 2 lety zemřel při nehodě jím pilotovaného vrtulníku. Rukopis nadšence pro letadla však firmě zůstal.
V zasedací místnosti jsou křesílka z nýtovaného plechu, jako měla řada válečných letadel, pod podhledem, který je podsvícenou černobílou fototapetou s výjevem americko-japonského vzdušného souboje visí svítidla, jejichž žebra jsou podobná těm, které se využívala pro výztuhu křídel. V kancelářích jsou pak napodobeniny kovových nýtovaných křídel jako pracovní stoly. Nábytek zase připomíná vybavení známé z kuchyněk letounů.
Výrobky z Plzně letečtí cestovatelé potkávají běžně, aniž by o to věděli
„S našimi výrobky pro letecký průmysl se mohou lidé potkat v interiérech letadel. Největší část komponentů, které vyrábíme, se používá v Airbus 320. Když nastupujete do letadla jdete kolem kuchyňky. Například dorazy vozíků, odpadkové koše, části boxů, které jsou zasunuté v kompletu kuchyňky, lišty, po kterých palubní personál zasunuje vozíky na místo, části kávovarů, … to vše děláme tady. Můžu říct, jsme vyrobili tisíce typů dílů, které se používají v letadlech Airbus a Boeing. Dalším příkladem, který mne teď napadl jsou desky pultu ovládacích panelů pro rozsvěcení světel a přístrojů, kde jsou jednotlivé ovladače popsány. To děláme speciální technologií, kdy tiskneme přímo do povrchu hliníku. Je to otěru vzdorná technologie, která může vydržet až několik desítek let,“ dodal Heckel. Prozradil také, že firma testuje novou úpravu povrchu, která by zajistila její antibakteriálnost. Ta by mohla vydržet až několik let.
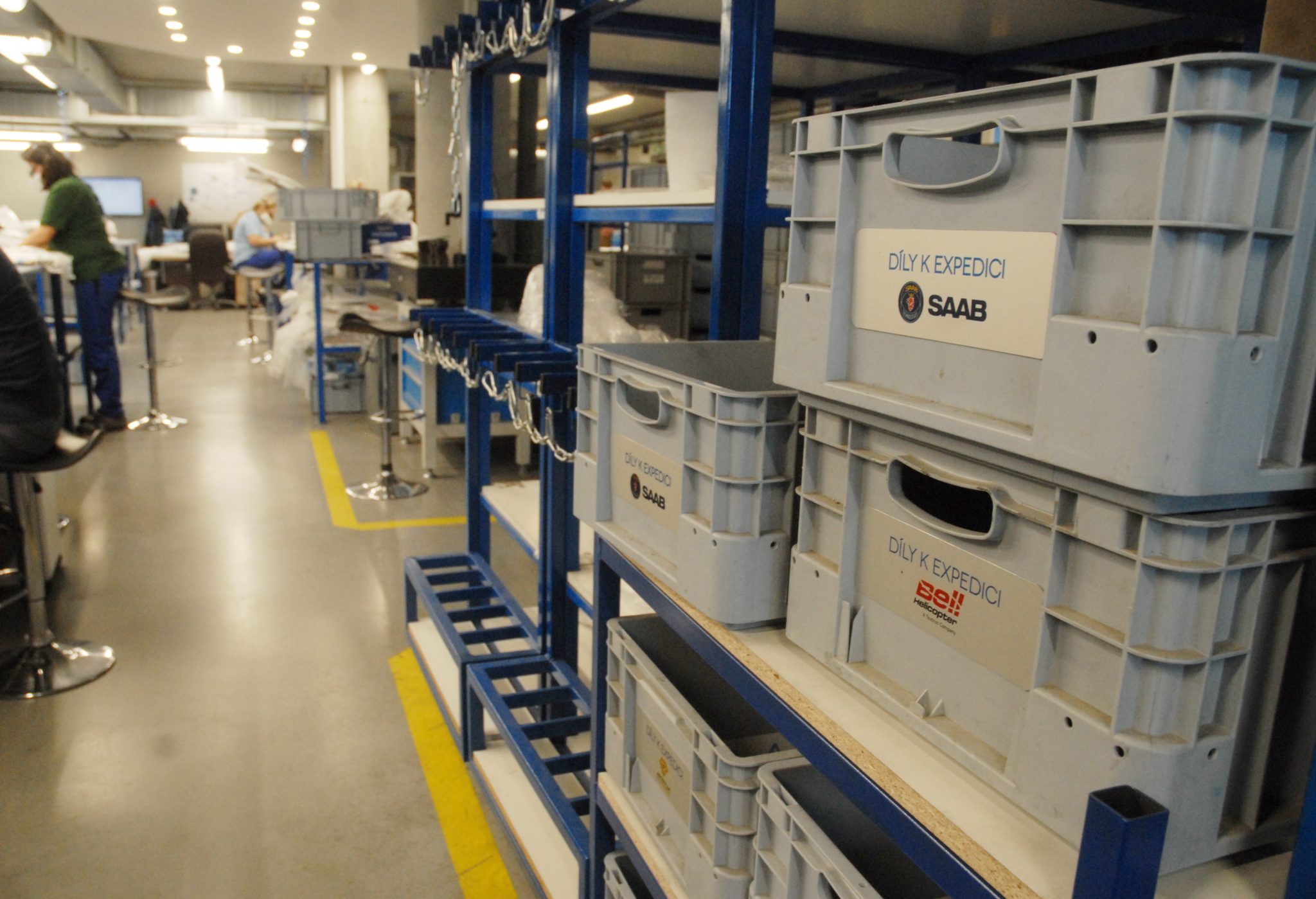
Letecký průmysl se vrací k normálu, masky jsou však novou divizí
Lze tedy konstatovat, že jarní koronavirová pandemie a nutnost chránit zaměstnance, aby nebyla ohrožena budoucnost firmy, odstartovala ve WPA novou divizi. Ta původní – výroba leteckých dílů se nezastavila, ale poklesla. „Kompletace letadla je složitá záležitost, výrobce potřebuje ohromné množství dílů. Navíc letadla se neobjednávají tak, že zákazník očekává jejich dodání za měsíc, ale počítá s roky. Spíš byl tedy problém v tom, že firmy omezily provoz kvůli problémům v dodavatelském řetězci, než že by neměli objednávky na letadla. Pokud vím, tak Airbus má objednávky asi na 5.000 A 320 a Boeing se strojem 737 má asi 4 tisíce objednávek. To znamená, že práce bude dost. Nyní jsme zhruba na 70 % stavu před koronakrizí,“ dodává. Svět se podle něj začíná postupně do normálu a lidé se musí naučit s koronavirem žít. „Ukazuje se, že lidé budou chtít cestovat, neodpustí si dovolenou a začnou zase cestovat,“ míní Jiří Heckel.
Za týden „skočily“ požadavky na desetitisíce masek a 130 tisíc filtrů
Zatímco s výroba pro letecký průmysl postupně nabíhá, segment ochranných masek jede na plné obrátky. „V tuto chvíli vyrábíme 4.500 masek denně, jsme schopni během několika dnů rozšířit kapacity až na 30.000 za den. Od začátku bylo cílem mít takovou technologii výroby, aby se daly vyrábět desetitisíce kusů denně. 3D tisk tedy nepřicházel v úvahu. Musela to být tedy rychlá výroba, proto jsme se rozhodli využít termoplastický elastomer, který se rychle přizpůsobuje formě a na rozdíl od silikonu, který používá jiný výrobce, se nemusí dlouho čekat na zatuhnutí ve formě. Navíc v něm nekondenzuje vlhkost jako v silikonu lze jej čistit dezinfekcí na bázi alkoholu,“ dodává Jiří Heckel. V druhé vlně koronavirové nákazy se firmě nashromáždilo velké množství objednávek „Lidé v jednom týdnu objednali 40.000 masek a 130 tisíc filtrů. Jsme sice pružní, ale takové množství jsme nečekali, takže někteří mohli čekat déle, než předpokládali a začali být nervózní. Věřím, že otevřením další dílny na kompletaci se podaří vysokou poptávku uspokojit,“ dodává Heckel. Firma také jedná se zahraničními zákazníky. „Naše masky teď testují hasiči v Bostonu, jednáme se zájemci z Londýna a řady dalších zemí,“ vypočítává Heckel. Firma je také účastníkem tendru ministerstva vnitra na dodávku několika desítek tisíc masek. (Předpokládaná hodnota veřejné zakázky je 22,5 milionu korun bez DPH. Termín podání nabídek byl 9. listopadu. Vnitro poptávalo 30 000 kusů polomasek.)
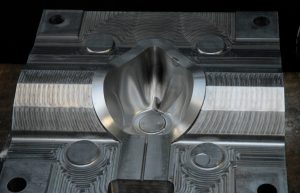
„V současné době máme vyrobeno přes 60 forem. Na každou velikost je potřeba jiná, stejně jako na jednotlivé součásti polomasek. Pokud započítáme skutečnost, že pokud na masce něco zásadního změníme, musí se změnit i forma, tak ta čísla naskáčou. Přitom běžně vyrobit formu na tento typ výrobků trvalo i půl roku,“ osvětluje ředitel WPA Jiří Heckel. Když na jaře zjistili, že je problém sehnat i filtry do masek, rozhodli se je také vyrábět sami. „Dnes máme stroj, který skládá filtrační materiál a roboty, které pak filtry kompletují. Filtry jsme opatřili ochrannou PET vrstvou, která zabraňuje jejich poškození. Nechali jsme je testovat ve Výzkumném ústavu bezpečnosti práce a vyplynulo z toho, že mají účinnost 99,995 %, což je o dva řády výše než FFP3, která běžně stojí mezi 200-300 korunami. Takže náklady na naši polomasku se za pár dnů vyplatí, jelikož FFP 3 respirátor můžete použít jen jednou,“ vypočítává Heckel.
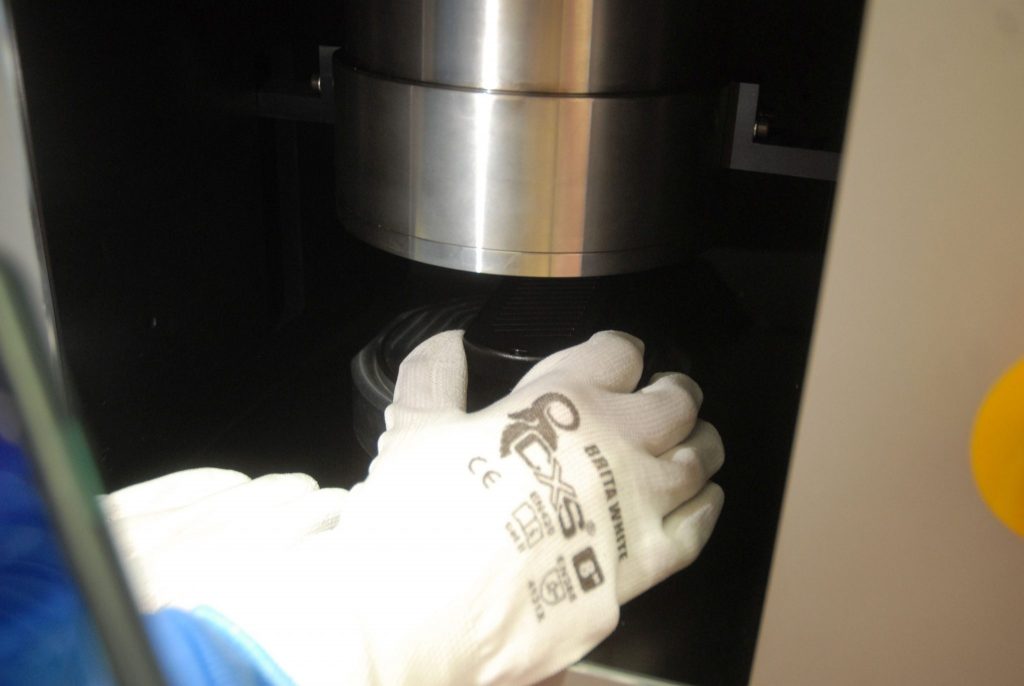
Firma pořídila vlastní testovací stroje, kterými kontroluje, jestli vyrobené filtry splňují udávanou účinnost. Při certifikačních měřeních se podle Heckela prokázalo, že největší problém respirátorů je jejich těsnost kolem obličeje. „U běžně dostupných respirátorů s označením KN 95 je v některých případech únik až 60 %. Náš termoplastický elastomer perfektně přilne na obličej a dýcháním se ještě více „přisaje“. Úniky byly v desetinách procenta,“ dodává Heckel. Nádechové filtry s vysokou účinností se dají v masce otáčet podle potřeby jejího uživatele.
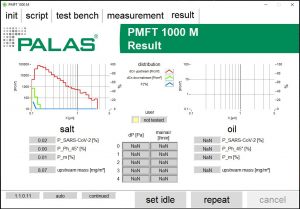
Investice přes 100 milionů. I přes „zakleknutí“
Není bez zajímavosti, že WPA je jednou z firem, na které „zaklekl“ finanční úřad a vyměřil jim vysokou pokutu. Nepomohla ani odvolání k nadřízeným orgánům. Firma musela zaplatit 21 milionů korun.. Spor o to, zda je pokuta oprávněná nyní čeká na projednání před Nejvyšším správním soudem.
I přes tyto problémy Heckel říká, že do vývoje polomasky a filtrů investovala společnost už přes 100 milionů korun. „Maska má za sebou také zhruba přes 100 modifikací od prvních prototypů,“ upřesňuje. Korpusy masek lze zakoupit v různých barvách. Firma Ekonomickému deníku představila nové barvy pro složky IZS a Armádu ČR.
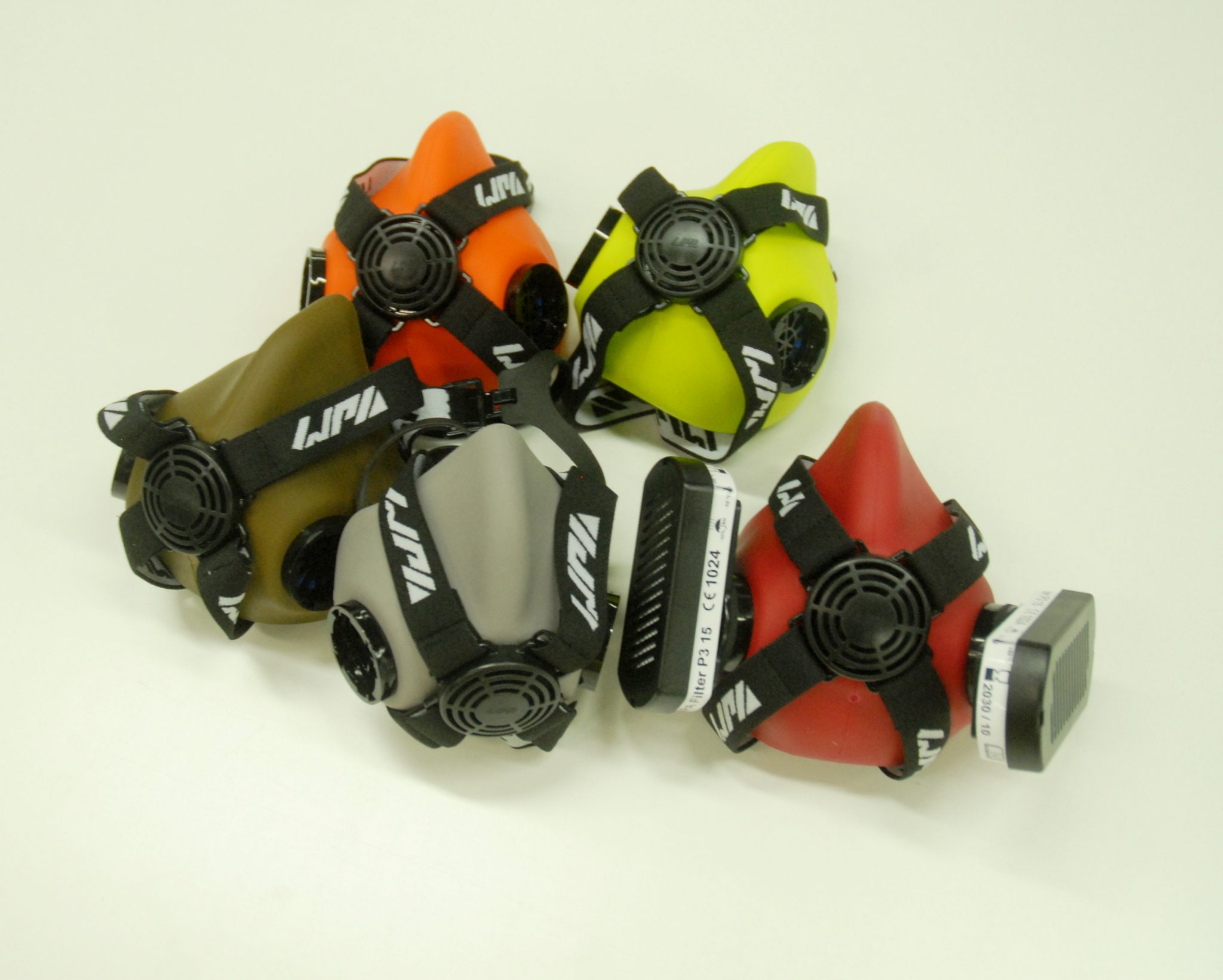
„Pokud chceme novou barvu, tu také musíme otestovat a nechat certifikovat. Tady ukazujeme praktické využití pro jednotlivé specializované složky,“ dodává mediální zástupce společnosti Roman Kraus. Kromě barev se dají „personifikovat“ také pruženky, neboli gumové popruhy, které masku drží na obličeji. „Nedávno jsme dělali značkové pro jednu velkou přepravní společnost,“ dodává Heckel.
Dotace? Dali jsme víc na kafe zaměstnancům, než jsme dostali
Vzhledem k inovativní technologii, změně výrobního procesu a do jisté míry strategické výrobě pro pomoc státu, které podle svých prohlášení podporuje ministerstvo průmyslu a obchodu se ptám, jestli firma získala nějakou podporu. „Systémy podpory jsou velice složité. Navíc si firma musí brát specifický typ úvěru, který není zcela výhodný. Veškeré investice se musí plánovat v závislosti na dotacích, což se neslučuje s naším stylem fungování, kde se snažíme co nejrychleji reagovat na změny. Pro zajímavost jsme za celou dobu fungování dali více za kafe či energetické nápoje pro naše zaměstnance, než jsme pobrali v dotacích,“ dodává Heckel.
Spolupráci s věznicí Bory si obě strany nemohou vynachválit
Firma už léta spolupracuje s vedením věznice v Plzni na Borech, která je kousek od sídla společnosti. Odsouzení zpracovávají díly pro letecký průmysl a po rozjetí výroby masek začali pracovat i na tomto produktu. „Je to oboustranně výhodná spolupráce. My jsme rádi, že máme stabilní kapacitu na zpracovávání našich zakázek od lidí, kteří si práce váží a snaží se ji dělat poctivě. Byl jsem příjemně překvapen kvalitou práce. Některé z nich jsme po propuštění zaměstnali,“ říká k tomu Heckel.
Ředitel plzeňské věznice Petr Vlk si spolupráci také pochvaluje. „Je to oboustranně výhodné. Někteří odsouzení pracují v areálu věznice na leteckých a automobilových zakázkách. Další pracují mimo areál věznice v nově zrekonstruované hale na kompletaci polomasek. Výroba se dál rozšiřuje a měli bychom tento týden otevírat další pracoviště. Na tuto práci jsme získali výjimku generálního ředitele vězeňské služby, protože standardně se zařazování na vnější pracoviště pozastavilo kvůli možnému nakažení odsouzených koronavirem a následným šířením ve věznicích. Vzhledem k tomu, že naši odsouzení po celou dobu práce mimo areál mají tyto polomasky, takže je zajištěna jejich maximální ochrana,“ říká Petr Vlk. Toto pracoviště by podle něj mělo být úzce vězeňské, aby se minimalizovala možná nákaza vězňů z „vnějšího světa“. „Pro WPA pracuje na zakázkách pro letecký průmysl 40 odsouzených, na kompletaci masek 20 a pro rozšíření počítáme s jednou směnou s 30 odsouzenými. Otázkou je, jestli bude potřeba nasadit i další směnu, to by pak počet stoupl,“ upřesnil ředitel věznice Plzeň Petr Vlk.
Jeho kolegové ze zdravotnického střediska dostali na začátku nějaké polomasky na testování, posléze je Vlk nakoupil i pro ty, kteří jsou v dozorčí a strážní službě. „Máme na ně dobrou zpětnou vazbu. Kolegové si pochvalují, že se nepotí, nevznikají aerosoly, které by se srážely v masce,“ dodává Petr Vlk.
Nový filtr pro výdechový ventil masku ještě vylepší
Posledním vylepšením masky bude filtr na výdechovou část, kde je nyní speciálně navržená membrána. „Máme několik ohlasů, že je potřeba udělat filtraci nejen nádechovou, kterou máme nyní, ale i výdechovou, proto už máme připravené řešení, které odstraní i tuto připomínku,“ upřesňuje Heckel. Podle něj bude tato varianta dostupná během několika dní. Firma připraví i „set“ výdechového filtru s popruhy, který půjde snadno nainstalovat i do předchozích modelů masek.
Jiří Reichl