Americká divize automobilky Toyota Motor spolu s firmou FuelCell Energy dokončily na Long Beach první „Tri-gen“ systém, který z bioplynu vyrábí ekologickou elektřinu, vodík a vodu. Obě společnosti uzavřely vzájemný kontrakt na dvacet let. Automobilka zároveň kompletně mění přístup k výrobě vozidel. Začne využívat metodu monozukuri spojující dovednosti zaměstnanců, moderní technologie a digitální postupy. To by mělo postupně přinést padesátiprocentní úsporu investic do vybavení, zkrácení doby přípravy výroby na polovinu a pětinový nárůst produktivity.
Společnost Toyota Logistic Services (TLS) Long Beach se stane prvním přístavním provozem, který bude kompletně poháněný přímo na místě generovanou energií z obnovitelných zdrojů. „Využíváním pouze obnovitelné výroby vodíku a elektřiny bude TLS Long Beach razit cestu i pro další naše provozy v různých částech světa,“ uvedl administrativní ředitel Toyoty Chris Reynolds.
Inovativní technologie palivových článků společnosti FuelCell Energy bude pro Toyotu v přístavu vyrábět energii prostřednictvím elektrochemického procesu, který přeměňuje bioplyn na elektřinu, vodík a použitelnou vodu vysoce účinným procesem bez spalování. Při něm prakticky nevypouští žádné látky znečišťující ovzduší.
Tri-gen vyrábí 2,3 megawattu obnovitelné elektřiny, z čehož část odebere TLS Long Beach na podporu svých operací v přístavu, který ročně zpracovává přibližně 200 tisíc nových vozů Toyota a Lexus.
Systém FuelCell Energy Tri-gen dokáže produkovat až 1200 kg vodíku za den, což pokryje potřeby TLS Long Beach v souvislosti s příchodem vodíkového modelu Mirai a zároveň bude dodávat vodík do blízké vodíkové tankovací stanice na podporu TLS logistiky a odvodňovacích operací v přístavu. Produkci vodíku bude možné zvyšovat a snižovat na základě aktuálních potřeb.
Denně bude koprodukováno z procesu výroby vodíku1400 galonů vody, která se využije společností TLS Long Beach pro mytí vozidel. To pomůže snížit využívání omezených místních dodávek vody o přibližně půl milionu galonů ročně.
Toyota mění výrobu, pomůže jí filozofie monozukuri
Automobilka Toyota plánuje kompletní změnu přístupu k výrobě automobilů. Začne přitom využívat metodu monozukuri spojující dovednosti zaměstnanců, moderní technologie a digitální postupy. Tato změna by měla postupně přinést padesátiprocentní úsporu investic do vybavení, zkrácení doby přípravy výroby na polovinu a pětinový nárůst produktivity. Monozukuri chce Toyota uplatnit mimo jiné v nové továrně na elektromobily. „Chceme změnit budoucnost bateriových elektromobilů, kdy proměníme samotné automobily, výrobu i způsob práce,“ uvedl prezident závodu BEV Factory Toyoty Takero Kato.
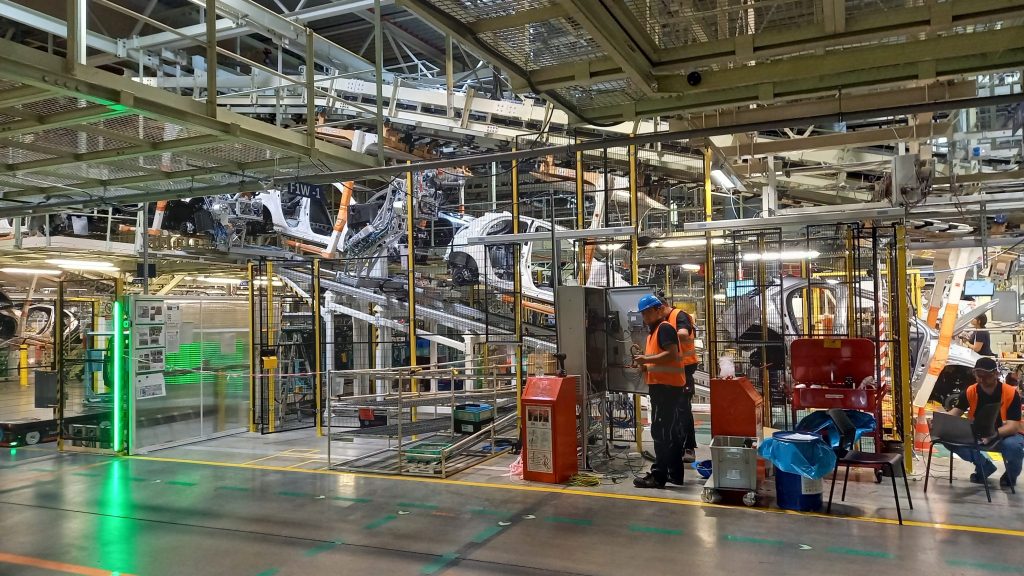
Na člověka zaměřený přístup monozukuri v Toyotě zavedl její zakladatel Kiičiro Toyoda. Jeho heslem bylo „děláme věci ku prospěchu ostatním“. Na základech této filozofie se zrodil jedinečný systém výroby TPS (Toyota Production System), jehož cílem je maximalizovat využívání lidských zdrojů ke zkrácení přípravné fáze a neustále zdokonalovat aktivity jidoka, tedy „automatizace s lidským dotekem“.
TPS se zaměřuje na zkracování přípravných fází, což pak usnadňuje hledání problémů a současně podporuje aktivity kaizen, což znamená „průběžné zlepšování“. Monozukuri je jedinečným atributem Toyoty a tvoří základ firemní snahy urychlit budoucnost výroby automobilů. Automobilka je přesvědčena, že pro budoucnost výroby je nezbytné rozvíjet filozofii monozukuri spojováním průběžně zdokonalovaných a na člověka zaměřených zásad nejlepší praxe s digitálními nástroji a pokrokovými technologiemi.
Toyota tak už od svého vzniku chce, aby pracovníci výrobních linek přímo v závodu sdíleli své dovednosti, vynalézavost a um s cílem vytvářet a zajistit masovou výrobu nových produktů. Tento postup pokračuje až do dnešních dnů, kdy jej podporuje i nově vzniklá ‚start-up dílna‘, kde se mohou pracovníci podělit o své poznatky, jak rychle reagovat na výzvy spojené s novými výrobními procesy případně sdílet své nápady.
Toyota zaměstnává řadu mimořádně zkušených řemeslných mistrů, které označuje Takumi. Díky jejich pečlivé práci se chlubí finální úpravou produktů na kvalitativní úrovni, která přesahuje současné možnosti nejlepších robotů.
Jelikož mnoho dovedností mistrů Takumi je postaveno na nikde nepopsaných praktických zkušenostech, jejich předávání dalším generacím je samo o sobě výzvou. Toyota proto pomocí digitálních technologií tvoří vizualizace praktických dovedností řemeslných mistrů ve snaze je srozumitelně vysvětlovat nové generaci s tím, že dovednosti se do budoucna možná podaří automatizovat.

Tento přístup už teď vede ke vzniku nových postupů výroby a zpracování. Technici Takumi například mohou s využitím pokročilých technologií zpracování realizovat mimořádně jedinečné návrhy, jejichž výroba byla doposud považována za příliš komplikovanou.
Digitální dvojník zkracuje přípravnou fázi výroby
S využitím digitálních nástrojů automobilka zároveň zkracuje přípravné fáze výroby vybavení a zvyšuje produktivitu stávajících provozů. Využívá k tomu digitální 3D modely, které slouží k odhalování nečekaných závad a problémů s výrobním vybavením. Ty by jinak mohly vést k prodloužení přípravných fází včetně změn návrhu a nutných přepracování. Přítomnost digitálního dvojníka kromě toho zkracuje přípravnou fázi výroby na polovinu.
Zlepšování efektivity, zvyšování produktivity a zkracování přípravných fází patří k nejsilnějším stránkám TPS. Díky tomu Toyota dokáže identifikovat a rychle zavádět úspěšná řešení k optimalizaci sériové výroby bateriových elektromobilů příští generace. Cílem je odbourat polovinu procesů a o polovinu snížit investice do výrobního vybavení prostřednictvím nové technologie odlévání ‚Gigacast‘ a samohybné výrobní linky. Ta zahrnuje tlakové odlévání hliníku, díky němuž se podařilo odbourat celou řadu dílů a procesů. Je koncipována jako trojdílná modulární architektura, jejíž předností je realizace výrobních a montážních činností v otevřeném prostředí.
Nasazením této jedinečné architektury společně s novým používáním licích forem chce Toyota dosáhnout dvacetiprocentní zlepšení produktivity oproti stávajícím odvětvovým standardům.
Na vybraných svařovacích linkách závodu Motomači se už zavádí koncepce samohybné linky, která je základem budoucího rozvoje a implementace výroby vozidel nové generace. Nová technologie vnitropodnikové dopravy výrazně zvyšuje flexibilitu uspořádání linky díky absenci klasických dopravníků. Tím se snižují nutné investice do závodu a zkracuje přípravná fáze výroby. Samohybná částečně smontovaná vozidla se bezpečně pohybují rychlostí sladěnou s rychlostí sériové výroby.
Nová generace baterií s kapalným elektrolytem
Toyota zároveň plánuje v letech 2026 až 2027 uvést novou generaci baterií ‚Popularisation‘ s kapalným elektrolytem. Konstrukce nových baterií přináší vysokou kvalitu za nižších nákladů díky používání lithium-železo-fosfátu (LiFePO) jako základního materiálu.
V letech 2027 až 2028 pak bude připravena uvést na trh svoji první baterii s pevnofázovým elektrolytem. Zde putují ionty látkou v pevném skupenství. Je tudíž nutné zajistit těsné spojení anody, katody a tuhého elektrolytu bez jakýchkoli mezer. Toyota s využitím pokrokového mechanismu a technologie synchronního řízení navrhla postup vysokorychlostního a vysoce přesného skládání baterií bez rizika poškození různých materiálů.
(mig)